ОБОСНОВАНИЕ ПРОМЫШЛЕННОЙ БЕЗОПАСНОСТИ НА ПРИМЕРЕ ОПАСНОГО ПРОИЗВОДСТВЕННОГО ОБЪЕКТА – ГАЗОРАСПРЕДЕЛИТЕЛЬНАЯ СТАНЦИЯ
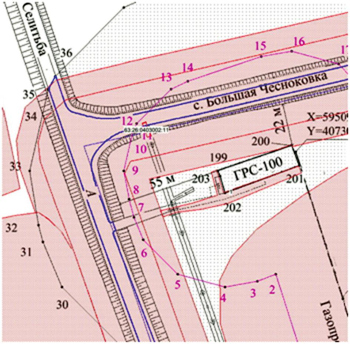
Опасный производственный объект ГРС введен в эксплуатацию в 1985 г. ГРС имеет один выходной коллектор и обеспечивает природным газом сельское поселение.
Объект нарушений, попадающий в зону минимально допустимых расстояний, установленных СП 36.13330.2012 «Магистральные трубопроводы. Актуализированная редакция СНиП 2.05.0685*», по объекту капитального ремонта – автодорога IV категории, расположена в 24 метрах от ограждения ГРС.
Нормативное расстояние от автодороги IV категории до ГРС с номинальным диаметром входного газопровода 300 мм и менее составляет не менее 50 м согласно СП 36.13330.2012, табл. 5, поз. 6.
1. Проведение анализа риска в части нарушения минимального расстояния. Определение сценариев возможных аварий. Оценка масштабов последствий возможных аварий. Оценка количества пострадавших в результате возможных аварий.
2. Моделирование аварийных ситуаций на трубопроводе с использованием программного комплекса Токси+Risk (версия 5), на основе методик СТО Газпром 2-2.3-400-2009.
3. Разработка рекомендаций и мероприятий, направленных на снижение уровня риска. Первоочередные меры:
- Выполнение обхода трассы подводящего газопровода-отвода с переносным газоанализатором 1 раз в неделю.
- Установка дополнительных знаков обозначения трассы газопровода в местах нарушения зон минимально допустимых расстояний.
- Выполнение плановых диагностических обследований ГРС не реже 1 раза в 5 лет.
- Проведение разъяснительных работ с населением и органами местного самоуправления через средства массовой информации не реже 2 раз в год.
- Проведение мероприятий по профессиональной и противоаварийной подготовке производственного персонала, обучение его действиям при возникновении нештатных ситуаций на подводящем газопроводе-отводе и ГРС.
- Проведение совместных противоаварийных тренировок с населением.
Перспективные меры:
- Демонтировать со стороны автодороги запроектированное ограждение ГРС, выполненное из металлических решетчатых панелей высотой 2,2 м.
- С целью снижения уровня риска взамен металлического ограждения возвести монолитное бетонное ограждение ГРС высотой не менее 2,2 м. состороны автодороги.
- Оснастить входной газопровод ГРС краном с системой автоматического закрытия.
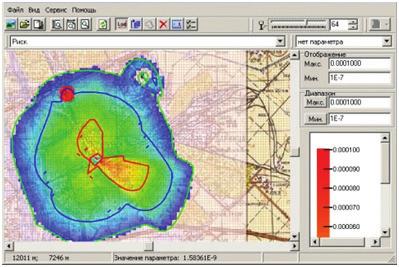
4. Анализ риска после проведения мероприятий, направленных на уменьшение масштаба последствий возможных аварий и количества пострадавших.
5. Разработка обоснования безопасности для эксплуатации действующего опасного производственного объекта в связи с имеющимся нарушением зоны минимальных расстояний, установленных в СП 36.13330.2012 «Актуализированная редакция СНиП 2.05.06-85*. Магистральные трубопроводы».
6. Сдача заключения экспертизы промышленной безопасности обоснования ОПО в Ростехнадзор с последующим внесением в Реестр.
7. Разработка проектной документации защитного ограждения ГРС на основании отчёта и заключения ЭПБ по обоснованию безопасности ОПО ГРС.
8. Возведение монолитного бетонного ограждения ГРС со стороны автодороги с целью снижения уровня риска для водителей и пассажиров автотранспортных средств автодороги IV категории.
КОМПЛЕКСНОЕ ДИАГНОСТИРОВАНИЕ ГАЗОПРОВОДОВ, НЕ ПРЕДНАЗНАЧЕННЫХ ДЛЯ ВНУТРИТРУБНОЙ ДИАГНОСТИКИ
Газопроводы являются важной составляющей газотранспортной системы. Они, как правило, являются однониточными, что накладывает на эксплуатирующую организацию серьезные ограничения по проведению ремонтных работ.
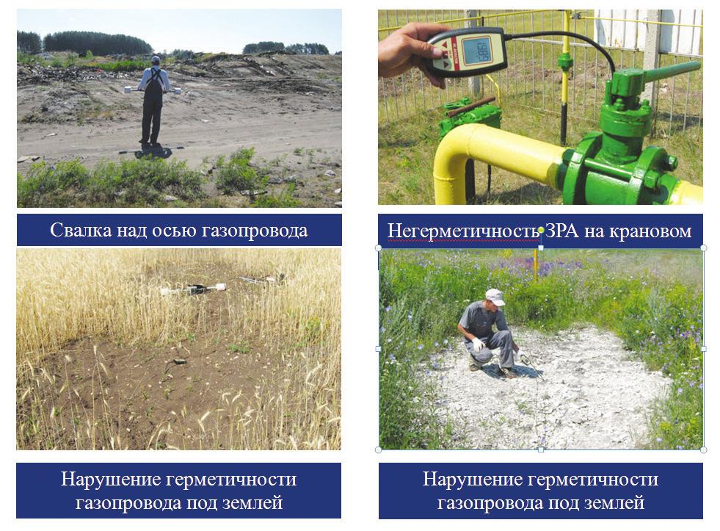
Газопроводы относятся к объектам, на которых внутритрубная дефектоскопия в настоящее время не проводится по следующим причинам:
- большое количество неравнопроходной арматуры, переходов, отводов;
- отсутствие камер приема и запуска очистных устройств;
- отсутствие подходящих снарядов-дефектоскопов (малых диаметров);
Наиболее распространенные дефекты, выявляемые при комплексном диагностировании газопроводов:
- ненормативная глубина залегания, местами встречаются открытые участки газопровода;
- размыв и обрушение краев оврагов, с выходом газопровода на поверхность;
- нарушение охранной зоны газопровода;
- расположение свалок над осью газопровода;
- трасса газопровода-отвода не расчищена от кустарников и поросли деревьев;
- нарушение герметичности газопровода по отношению к внешней среде;
- нарушение герметичности ЗРА на линейных участках газопровода;
- отсутствие защитных кожухов на переходах через автомобильные дороги;
- локальные повреждения изоляционного покрытия.
Нарушение герметичности происходит по следующим причинам:
- сквозные трещины в продольных и кольцевых швах заводского изготовления, возникающие в процессе эксплуатации;
- сквозная коррозия при неправильно функционирующих средствах ЭХЗ;
- пропущенные и развивающиеся дефекты в кольцевых швах, выполненных при строительстве.
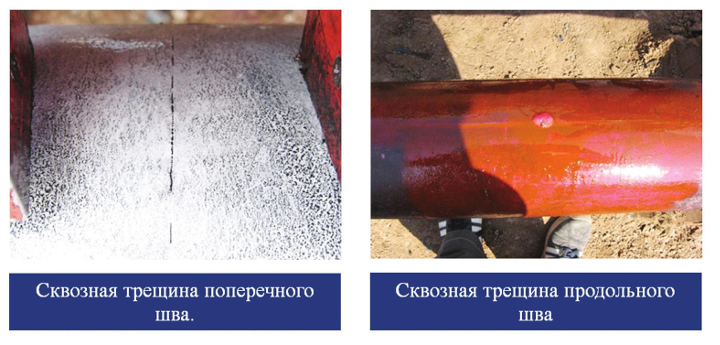
В результате проведенных исследований установлено, что продольные и кольцевые сварные соединения заводского изготовления с обнаруженными трещинами выполнены контактной сваркой.
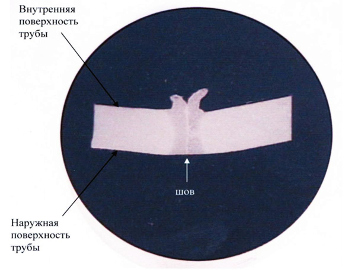
Данный способ представляет собой сварку металла путем его нагрева с помощью воздействия электрического тока очень большой силы (несколько тысяч ампер) под воздействием сжимающего давления.
Для выяснения причины образования трещин в заводских сварных соединениях, были проведены металлографические исследования на образцах, изъятых в ходе ремонтных работ из различных газопроводов.
Проведены испытания на статическое растяжения и ударный изгиб образцов с кольцевым сварным соединением.
Выводы: при изготовлении труб контактной сваркой в сварных соединениях концентрируются нерастворимые неметаллические включения – сульфиды размером 10 - 50 мкм, возникают микротрещины, как на поверхности, так и внутри сварного соединения.
В процессе эксплуатации, при воздействии статических и динамических нагрузок и естественного старения металла, происходит объединение микротрещин в магистральные, проходящие через все сечение сварного шва.
По результатам металлографических исследований можно сделать следующие выводы:
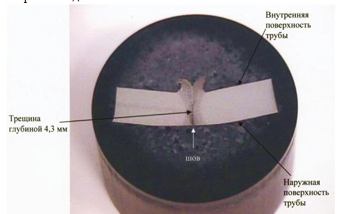
- Контактная сварка вносит существенное ослабление в конструкцию из-за существенного содержания в исследуемых образцах примесей серы и фосфора.
- Сера находится в стали главным образом в виде FeS. Это соединение сообщает стали хрупкость при высоких температурах, например при ковке или сварке, - свойство, которое называется красноломкостью. Сера понижает сопротивление усталости и уменьшает коррозионную стойкость.
- Фосфор образует с железом соединение Fe3P, которое растворяется в железе. Кристаллы этого химического соединения отличаются повышенной хрупкостью, располагаются по границам зерен стали, резко ослабляя связь между ними, вследствие чего сталь приобретает очень высокую хрупкость в холодном состоянии (хладноломкость). Особенно сказывается отрицательное влияние фосфора при высоком содержании углерода.
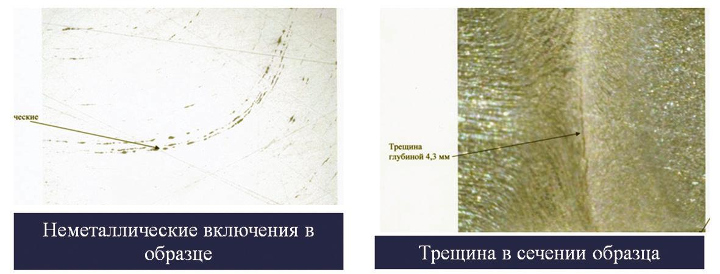
Дефектные стыки заводского изготовления встречались на газопроводах 1980 -1996 гг. ввода в эксплуатацию, см табл. 1.
Год ввода | Диаметр, мм | Толщина стенки, мм | Рабочее давление, кгс/см2 | Марка стали | Завод изготовитель |
1983 | 159 | 5 | 75 | Сталь 20 | ВПО «Союзтрубсталь» Таганский металлургический завод |
1980 | 219 | 7 | 17 | Сталь 10 | ОАО «Северский трубный завод» |
Сталь 20 | |||||
1986 | 159 | 5 | 75 | Сталь 10 | п/я В-8508 с. Полеской 3 Свердловской обл. |
1981 | 159 | 5 | 35 | Сталь 10сп | п/я Р6349 |
1996 | 219 | 6 | 75 | Сталь 10сп | Выксунский металлургический завод |
Таким образом, при проведении диагностики, можно уже на этапе анализа технической документации выявить потенциально опасные газопроводы и скорректировать программу технического диагностирования.
Специалистами НПЦ «Молния» создан диагностический комплекс М-1 для надземного контроля трубопроводов, обеспечивающий одновременно электрометрические и магнитометрические измерения и выполняющий функции нескольких приборов.
В комплексе «М-1» для бесконтактного диагностирования газопроводов объединены электрометрический и магнитометрический методы неразрушающего контроля, встроен GPS-приемник и акселерометр.
Комплекс позволяет в режиме реального времени, в процессе движения оператора вдоль оси газопровода, обеспечить контроль и запись всех измеряемых параметров, представляет на экране дисплея графическую и цифровую информацию о токе, индукции магнитного поля, глубине залегания газопровода.
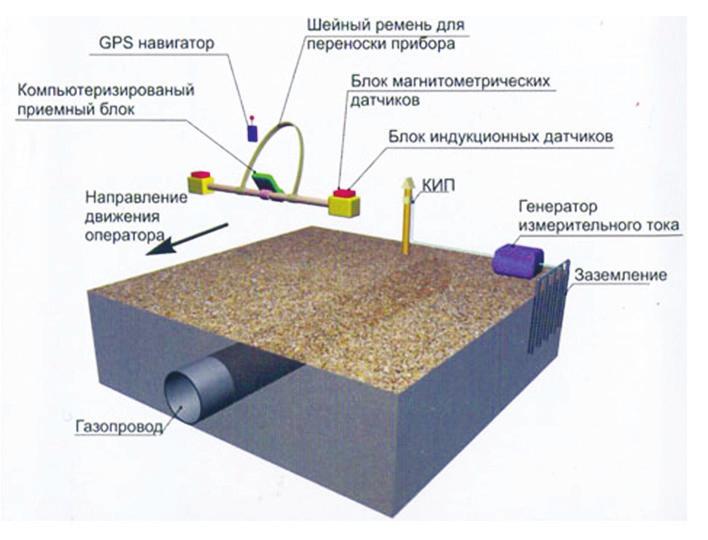
ОПЫТ ОЦЕНКИ ВОЗМОЖНОСТИ ЭКСПЛУАТАЦИИ СВАРНЫХ СОЕДИНЕНИЙ С ДЕФЕКТАМИ НА РАСПРЕДЕЛИТЕЛЬНЫХ ГАЗОПРОВОДАХ
Большинство сварных соединений газопроводов, сваренных по старым нормативам, не соответствуют действующим СТО и СНиП.
Наиболее часто встречающиеся дефекты: непровары в корне шва, шлаковые включения, поры. Такие сварные соединения подлежат либо ремонту, либо вырезке, что приводит к значительным экономическим и временным затратам.
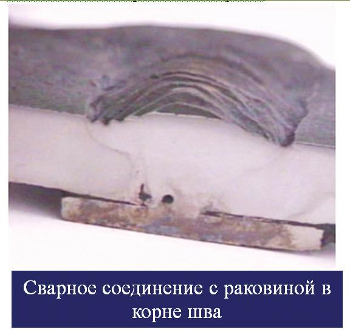
Одновременно с этим, согласно п.7.16 СТО Газпром 2-2.4-083-2006сварные соединения, забракованные по действующим нормам, могут быть оставлены в эксплуатации по результатам дополнительных прочностных расчетов, выполненных с учетом фактических свойств основного металла и сварных соединений, а также уровня нагруженности диагностируемого участка газопро- вода.
На гидравлических испытаниях катушка с кольцевым сварным соединением содержащим внутренние дефекты не соответствующие требованиям действующих НТД, выдержала давление 42 кгс/см2 в течение 12 часов, что превышает проектное давление в 3,5 раза.
Были проведены механические испытания на разрыв трёх образцов сварного соединения. Разрыв всех трёх образцов произошел вне сварного шва по основному металлу, притом, что в двух образцах металлография показала наличие внутренних дефектов сварного шва. Таким образом, было экспериментально доказано, что выявленные дефекты сварного шва не оказывают значительного влияния на прочность сварного соединения.
В результате проведенной дефектометрии (гидравлических испытаний образцов, лабораторных испытаний и теоретических расчетов), выявлено, что все обследованные сварные соединения имеют достаточный запас прочности и могут быть оставлены в эксплуатации на расчетный период времени.
В отличие от дефектоскопии, ставящей своей задачей обнаружение (выявление) дефектов, целью дефектометрии является определение параметров дефекта по экспериментальным данным с использованием алгоритмов решения обратных задач, что в настоящее время является эффективным средством диагностики, позволяющим обеспечить необходимую надежность ОПО при существенном снижении затрат на его эксплуатацию и ремонт.
РАСЧЕТ МЕТОДОМ КОНЕЧНЫХ ЭЛЕМЕНТОВ
Современная вычислительная техника позволяет проводить расчеты сооружений с более подробным описанием их внутренней структуры и с более точным учетом действующих нагрузок. Для этого разработаны специальные методы расчета, среди которых наибольшее распространение получил метод конечных элементов (МКЭ).
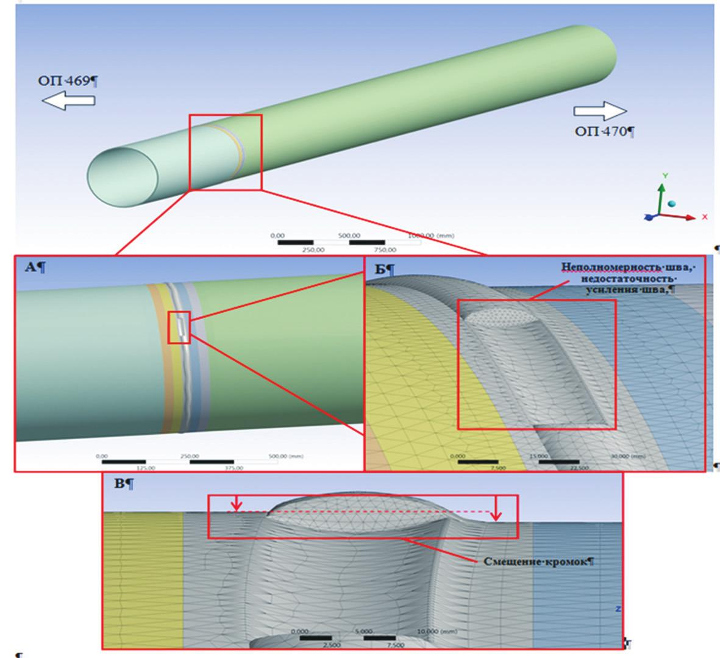
Метод конечных элементов – это метод расчета сооружений, основанный на рассмотрении сооружения как совокупности типовых элементов, называемых конечными элементами (КЭ).
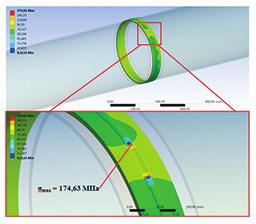
В настоящее время разработаны вычислительные комплексы, позволяющие рассчитывать на компьютере сложные и разнообразные сооружения на различные воздействия. К таким относятся расчетные комплексы NASTRAN, ANSIS, ЛИРА, СУМРАК и др.
Расчет проводится с целью оценки прочности наиболее дефектного участка газопровода. Соответственно при обеспечении статической прочности наиболее дефектного участка трубопровода, прочность остальных участков также будет обеспечена.
В этом методе сооружение делится на определенное число КЭ, соединяемых между собой в узлах конечно-элементной модели. А нагрузка, действующая на сооружение, переносится в узлы. Это позволяет определять НДС сооружения через узловые усилия и перемещения конечно-элементной модели.
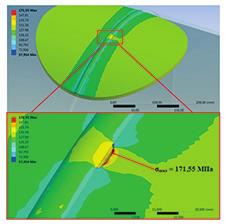
Модель дефектного участка (неполномерность шва 11М42, неравномерная форма шва, смещение кромок, недостаточность усиления):
А – 3D модель, Б – сетка конечных элементов, В – участок дефекта со смещением кромок и недостаточным усилением шва.
Анализ НДС проводился в программном комплексе Ansys, распределение эквивалентных напряжений в конструкции газопровода. Как видно из рисунка наибольшие напряжения возникают в дефектах «подрез» на сварном шве 5М27 и около дефекта «неполномерность шва, смещение кромок, недостаточность усиления» на сварном шве 11М42.
ОБСЛЕДОВАНИЕ ОБЪЕКТОВ, НЕ ВВЕДЕННЫХ В ЭКСПЛУАТАЦИЮ
Порядок приемки и ввода объекта, законченного строительством, в эксплуатацию регламентирован на сегодняшний день двумя документами:
- статьей 55 Градостроительного кодекса РФ;
- Положением об осуществлении ГСН в РФ, утвержденным, постановлением Правительства РФ от 1.02.06г. No54.
Согласно Градостроительному кодексу РФ разрешение на ввод объекта в эксплуатацию выдается органом, выдавшим разрешение на строительство. Заключение о соответствии (ЗОС) органа государственного строительного надзора выдается только в случае, если при строительстве не были допущены нарушения соответствия выполняемых работ требованиям нормативной технической документации и проекта, либо такие нарушения устранены до даты выдачи заключения о соответствии.
В случае, если объект или его часть построены с нарушением действующих нормативно-технических документов, либо установленного порядка строительства, застройщику потребуется выполнить силами независимой специализированной организации, имеющей соответствующую лицензию, детальное (инструментальное) обследование.
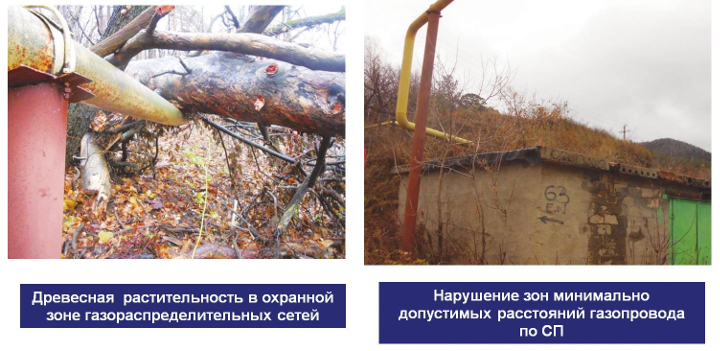
Целью обследования является оценка соответствия построенного, но не введенного в эксплуатацию объекта действующих нормативно-технических документов, выявление отклонений и определение технических решений для последующей реконструкции объекта.
По результатам отчета о техническом обследования , целью устранения выявленных несоответствий Проекторный организацией проводятся проектно-изыскательные работы и разрабатывается проект реконструкции объекта.
При положительной Государственной экспертизе Проекта реконструкции объекта выполняется сбор документов на производство строительно-монтажных работ.
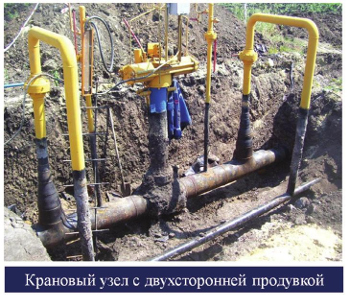
При выполнении обследования производятся следующие виды работ:
- Анализ проектной, исполнительной документации и другой технической документации, сбор вспомогательной информации;
- Позиционирование трассы газопровода по системе WGS-84, с указанием расположения технических устройств и элементов газопровода;
- Визуальный и измерительный контроль на всем протяжении надземного участка газопровода, включающий определение состояния лакокрасочного покрытия, опор, выявление дефектных участков и отклонения от действующей НТД, и участков с аномальной намагниченностью газопровода;
- Визуальный и измерительный контроль, ультразвуковая толщинометрия и измерение твердости основного металла в зонах термического влияния сварных швов элементов на всем протяжении над- земного участка газопровода;
- Магнитопорошковый и вихретоковый контроль основного металла, магнитопорошковый контроль продольных сварных соединений на дефектных участках надземного газопровода;
- Выборочный контроль качества кольцевых сварных соединений не менее 5% от общего количества сварных соедине- ний сваренных каждым сварщиком на объекте, из них 10% рентгенографическим;
- Контроль кольцевых сварных соединений в местах переходов через автодороги и в местах расположения компенсаторов линейных расширений;
- Обследование запорно-регулирующей арматуры: внешний осмотр наличия окраски, выявление раковин, трещин, коррозии и других дефектов, неразрушающий контроль основных элементов корпуса.
- Приборное диагностирование подземного участка газопровода включает в себя:
- А) измерение разности потенциалов «труба-земля» на КИПах и доступных местах, контроль исправности изолирующих фланцевых соединений;
- Б) определить удельное электрическое сопротивление грунта вдоль газопровода;
- В) определение влияния блуждающих токов газопровод;
- Г)определение состояния изоляционного покрытия и глубины залегания.
ДИАГНОСТИКА КРАНОВЫХ УЗЛОВ МАГИСТРАЛЬНЫХ ГАЗОПРОВОДОВ
Крановый узел предназначен для:
- Обеспечения проведения работ на линейной части МГ требующих отключения подачи газа.
- Отключения участков МГ в случае возникновения аварийных ситуаций.
Объектами диагностирования кранового узла являются запорно-регулирующая арматура (ЗРА), подземная технологическая обвязка кранового узла (байпасные и свечные линии, отводы, тройниковые соединения) и участки линейной части газопровода протяженностью 250 метров по обе стороны от кранового узла.
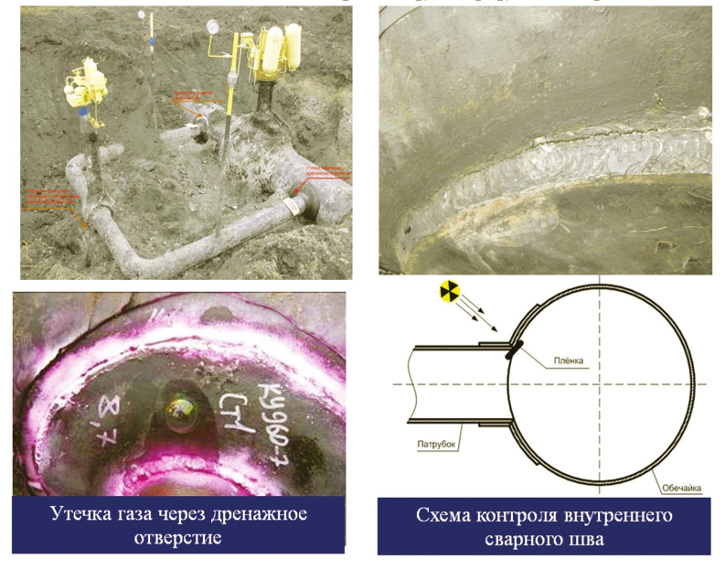
Наиболее опасными дефектами крановых узлов являются трещины в сварных швах тройниковых соединений.
Опыт проведения работ показывает, что около 5 % крановых узлов имеют критические дефекты в виде трещин сварных швов тройниковых соединений. Причиной возникновения трещин в тройниковых соединениях является поперечное перемещение байпасной линии относительно плоскости основной нитки, вызываемые просадкой грунта и разрушением опор.
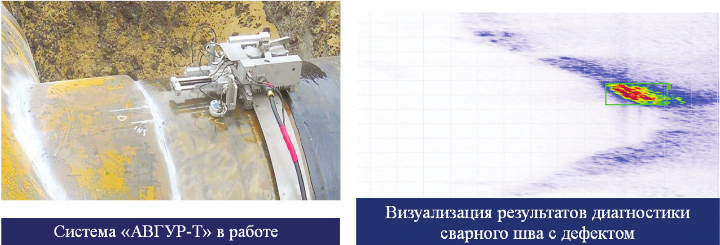
Фактором повышенного риска при диагностике крановых узлов является неконтролепригодность сварных соединений приварки патрубка к магистрали, находящихся под накладкой.
Проведение контроля таких сварных соединений традиционными методами ультразвуковой или рентгеновской дефектоскопии невозможно с наружной поверхности тройника, т.е без вырезки оборудования из трассы.
Для решения задачи контроля угловых сварных соединений патрубков, находящихся под накладкой, НПЦ «МОЛНИЯ» использует автоматизированную систему ультразвукового контроля «АВГУР-Т».
АО НПЦ «МОЛНИЯ» провела ряд испытаний на специально созданных стендах, подтвердивших заявленные параметры системы, а именно обнаружение и определение размеров дефектов в виде трещин, непроваров, несплавлений и инородных включений.